Social Start-up baut Fahrräder aus Bambus
Ein Fahrrad aus Bambus – das ist etwas Besonderes. Im Falle des Kieler Start-ups my Boo nicht nur wegen des außergewöhnlichen Rahmenmaterials, sondern wegen des positiven Impacts seiner Produkte.
Manchmal braucht es nur eine Nachricht bei facebook, um etwas Großes in Bewegung zu setzen – das würde Maximilian Schay wahrscheinlich sofort unterschreiben. Es ist Ende 2012 als er eine solche Nachricht erhält. Sie stammt von einem Freund der zu der Zeit durch Ghana reist und zeigt ein Foto eines Bambusfahrrads. Maximilian ist gerade frisch an der Uni Kiel eingeschrieben und möchte BWL studieren. Zusammen mit seinem Kommilitonen und Freund Jonas Stolzke, hat er den Wunsch ein Unternehmen zu gründen, das einen echten Mehrwert für die Gesellschaft hat. An die Fahrradbranche hatten dabei beide allerdings nicht gedacht.
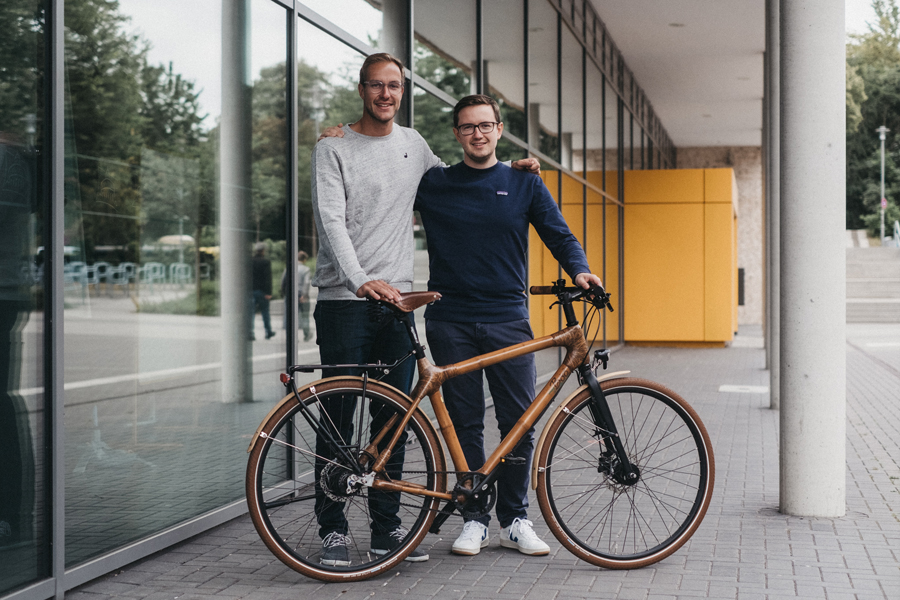
Jonas Stolzke (links) und Maximilian Schay / ©my Boo/Robert Strehler
Bambusfahrräder gibt es schon über 100 Jahre
Ein Fahrrad aus Bambus, das erregt erst einmal Aufsehen. Schließlich besteht ein Rahmen meist aus Aluminium oder Carbon. Erstaunlich, wenn man bedenkt, dass die Idee von Fahrradrahmen aus Bambus schon alt ist. „Bambusfahrräder gibt es schon über 100 Jahre. Das älteste Rad ist aus dem Jahr 1894 und wurde ganz anders gebaut als unsere Räder. Man hatte Muffen aus Metall, in die die Bambusrohre nur reingesteckt wurden“, erklärt Felix Habke, der sich seit 2013 um die Öffentlichkeitsarbeit des Start-ups kümmert.
Um die Bambusrohre zu einem Rahmen zu verbinden, nutzt my Boo eine Technik des US-Amerikaners Craig Calfee. Dabei werden die Rohre durch einige wenige Metallteile und Hanfseile zusammengehalten, die in Kunstharz getränkt werden. So entstehen die charakteristischen Knotenpunkte der Räder. „Calfee ist der Bambusfahrrad-Guru der Neuzeit. Er macht das bestimmt schon 15 Jahre und gibt weltweit Workshops zum Bau von Bambusfahrrädern“, sagt Habke.
Bambus wächst nämlich nicht nur in Asien, sondern in nahezu allen Gegenden rund um den Äquator. Aufgrund seiner dämpfenden Eigenschaften und natürlichen Stabilität, eignet er sich bestens für Fahrradrahmen. In Yonso, einem kleinen von Bambuswäldern umgebenen Dorf in Ghana, besuchte Kwabena Danso einen Workshop von Calfee. 2013 traf sich Danso zum ersten Mal mit Maximilian und Jonas.
Gegen Jugendarbeitslosigkeit, für mehr Bildung
Kwabena Danso erregte die Aufmerksamkeit der beiden Studenten mit seinem Yonso Project. „In dem Projekt geht es darum, die Jugendarbeitslosigkeit durch fair bezahlte Arbeitsplätze zu bekämpfen. Vorrangig soll in Bildung investiert werden, zum Beispiel durch Schulstipendien“, erklärt Felix Habke. Danso hat selbst von einem Bildungsstipendium profitiert und danach beschlossen, seinem Dorf etwas zurückgeben zu wollen. Die ersten Jahre finanzierte sich sein Projekt durch Spenden, die leider mit den Jahren immer weniger wurden. Sein Wunsch war, auch unabhängig von der Spendenbereitschaft Anderer, helfen zu können.
Das gemeinsame Treffen in Ghana wirkt bis heute nach: „Wir haben dort die Produktion aufgebaut, aber eigentlich ist es eine klassische Handelsbeziehung auf Augenhöhe. Wir lassen unsere Rahmen vor Ort fertigen und kaufen sie zu einem fairen Kurs ab“, so Habke. Aus anfangs drei Mitarbeitern sind inzwischen 40 geworden.
Das Ziel: Eine Schule für 1.000 Kinder
Die Region profitiert aber nicht nur durch die geschaffenen Arbeitsplätze. Ein Teil der Erlöse fließt zusätzlich in Bildungsprojekte. Anfangs wurden Schul-Starter-Kits für die Schüler*innen des Dorfes finanziert, aber diese Art der Förderung war für Maximilian und Jonas nicht langfristig genug. „Deshalb sagten wir: Okay, wir machen das anders. Wir zahlen jetzt pro Rad in einen Fond ein und Kwabena verfügt über diesen Fond. Damit können zwar weniger Kinder unterstützt werden, diese aber langfristiger“, erinnert sich Felix Habke. Ein erfolgreiches Modell, wie der Blick nach Yonso heute beweist: Im Oktober 2019 öffnete erstmals eine durch den Fond finanzierte Schule.
Derzeit besuchen gut 200 Kinder die neue Schule. Das Ziel ist eine Kapazität von 1.000 Schüler*innen. Für Kwabena Danso ging mit dieser Schule ein Traum in Erfüllung. „Am Anfang haben wir das nicht für realistisch gehalten“, räumt Habke ein. Jetzt hat my Boo zusätzlich noch einen Verein gegründet, der die Schule finanziell unterstützen soll. Durch eine betterplace-Kampagne ist die Finanzierung eines Schulbusses geplant.
Das Offensichtliche ist das Spannende
Obwohl der Bambusrahmen eigentlich nicht das Besondere an den my Boo Rädern ist, profitiert das Unternehmen von dem ungewöhnlichen Erscheinungsbild seiner Räder. „Es ist ein Icebreaker“, räumt Felix Habke ein. „Für die Leute ist erst einmal das Offensichtliche das Spannende. Man sieht es und weiß: Das ist etwas Besonderes.“ Die Geschichte dahinter ist wiederum interessant für den Fachhändler, so hat er ein überzeugendes Verkaufsargument für seine Kunden.
Aber wie steht es eigentlich um die Fairness der restlichen Radteile? „Tatsächlich ist es so, dass wir überall dort, wo wir Einfluss nehmen können, das auch tun“, erklärt Habke. Der Markt ist allerdings begrenzt, daher habe das Unternehmen nicht bei allen Teilen eine große Auswahl. „Am Ende des Tages geht es bei uns um den Rahmen, das ist unser USP. Den produzieren wir selbst und wissen, was dahintersteckt. Bei allen anderen Teilen versuchen wir immer den besten Partner zu finden“.
Text: Marisa Becker
Hinterlasse einen Kommentar
An der Diskussion beteiligen?Hinterlasse uns deinen Kommentar!